Okay, real talk here. I still remember the first time I sat down with my Singer sewing machine. I was so excited to dive into my first project – a simple tote bag that seemed foolproof. But then I opened up the manual and saw the threading diagram, and my brain basically went “nope.” Those little arrows and numbered steps might as well have been hieroglyphics.
Maybe you’re in that exact same boat right now. You’ve got your beautiful Singer sitting there, ready to create magic, but you’re staring at it like it’s some alien spacecraft. Trust me, I’ve been there. The good news? Learning how to thread a Singer sewing machine isn’t nearly as scary as it looks. I’m going to walk you through this step-by-step, and by the end, you’ll wonder why you ever stressed about it.
Table of Contents
Why This Matters More Than You Think
Before we jump into the nitty-gritty, let me tell you why getting your threading right is absolutely crucial. I learned this the hard way during my second sewing attempt (spoiler alert: it was a disaster).
When your threading is off, your machine basically throws a tantrum. You’ll get these awful bird’s nest tangles underneath your fabric, your stitches will look drunk, or worse – your machine will just sit there mocking you by refusing to stitch at all. I’ve definitely had moments where I wanted to chuck my Singer out the window because of threading issues.
But here’s what I discovered: when you thread your machine properly, it’s like having a conversation with an old friend. Everything flows smoothly, your stitches look professional, and you actually enjoy the process instead of fighting it.
Safety First (I Promise I’m Not Being Dramatic)
Alright, before we get our hands dirty, we need to talk safety. I know, I know – you’re probably thinking “it’s just threading, how dangerous can it be?” Well, let me tell you about the time my friend nearly took off her fingertip because she forgot to turn off her machine first. Not fun.
1. Turn That Thing Off!
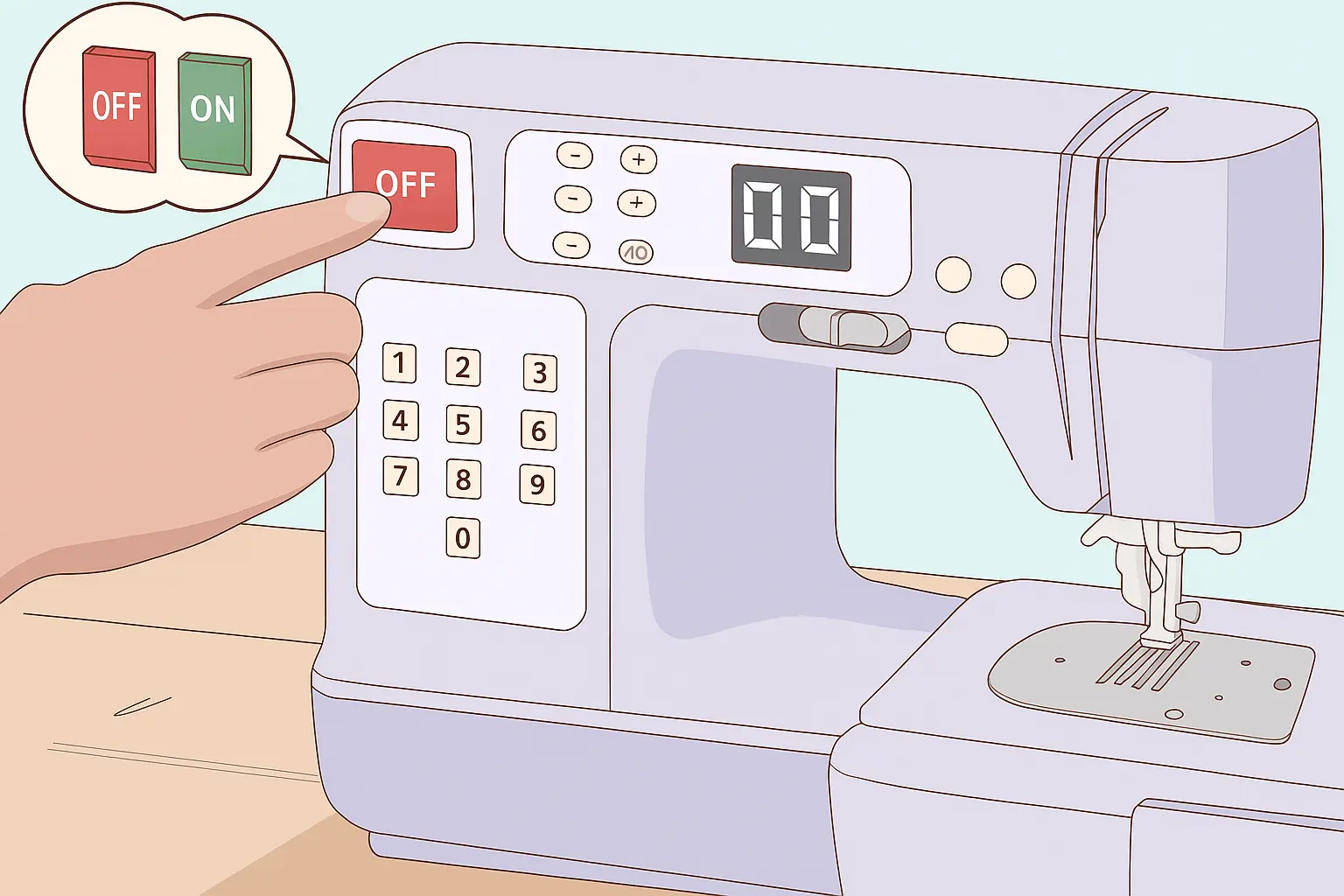
First things first – find that power switch and flip it off. I don’t care if you’re just “quickly checking something.” Your Singer is powerful, and those moving parts don’t mess around. I’ve made this mistake exactly once, and let me tell you, my heart rate definitely spiked when that needle started moving unexpectedly.
2. Get Your Needle Out of the Way
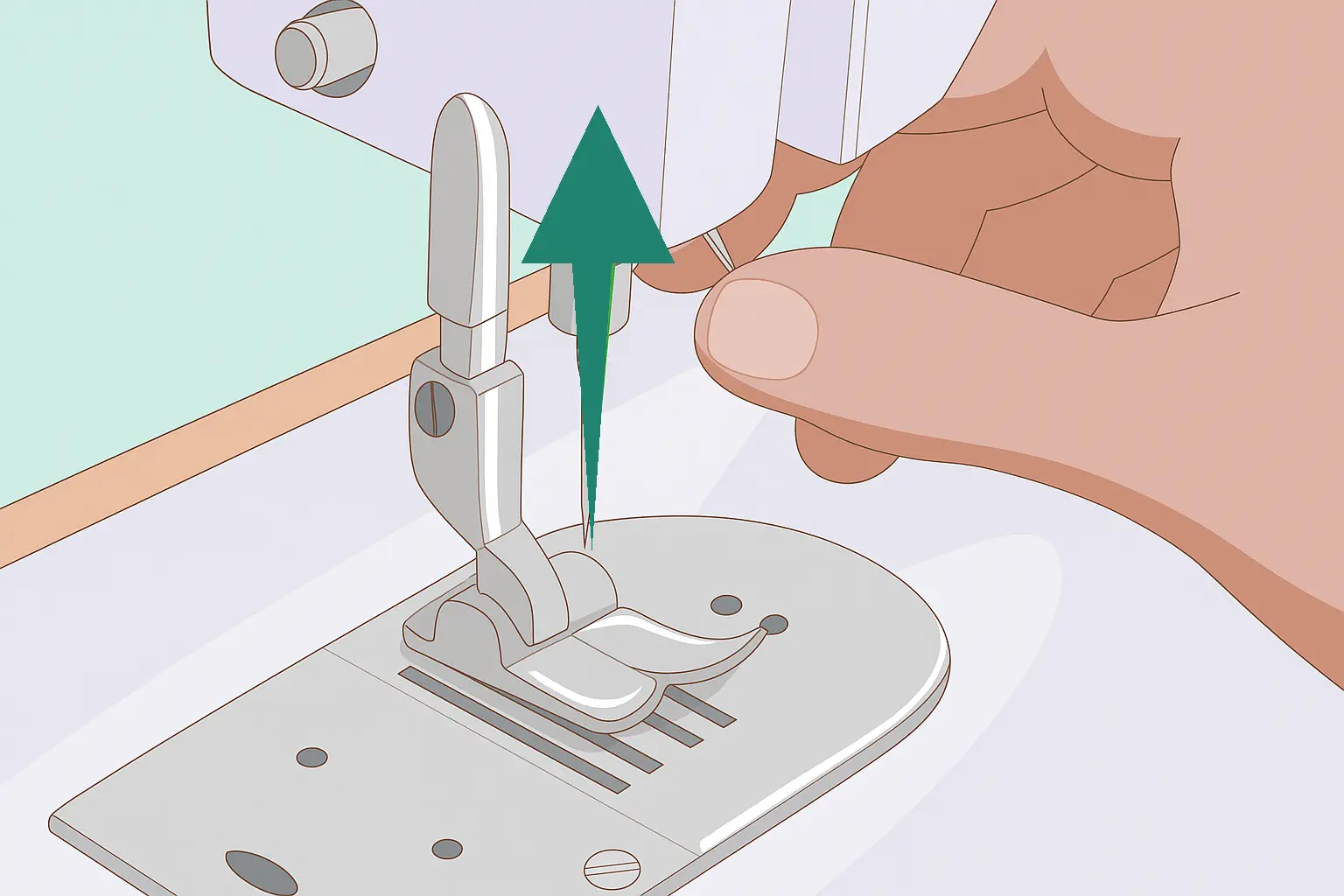
Now grab that hand wheel on the right side of your machine and turn it toward you (that’s clockwise, for those keeping track). Keep turning until your needle is at the very top – like, as high as it can possibly go. Think of it as giving yourself the maximum amount of workspace.
Here’s a rookie mistake I made early on: I kept turning the wheel past the highest point, and the needle started going back down. Don’t do that! Stop right at the peak. You’ll know you’ve hit it when the needle stops rising.
3. Lift That Presser Foot
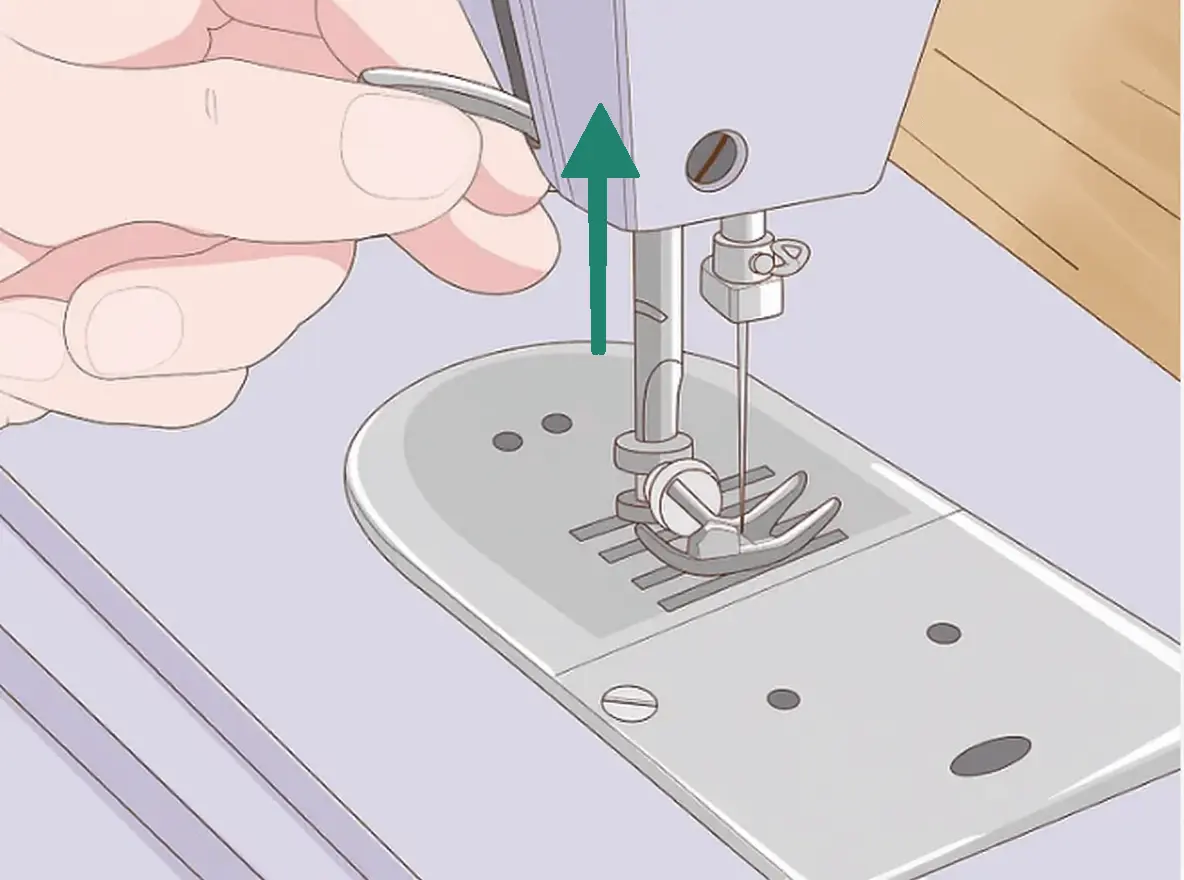
See that little lever next to your needle? Push it up to raise the presser foot. This is like clearing your desk before starting a big project – it just makes everything easier. Plus, having that foot up releases some tension in your machine, which makes threading so much smoother.
The Threading Adventure Begins
Okay, here we go! I’m going to be completely honest with you – this might take a few tries to get comfortable with. When I first learned this, I probably re-threaded my machine five times before it felt natural. That’s totally normal, so don’t get discouraged if it doesn’t click immediately.
Step 1: Sort Out Your Bobbin Situation
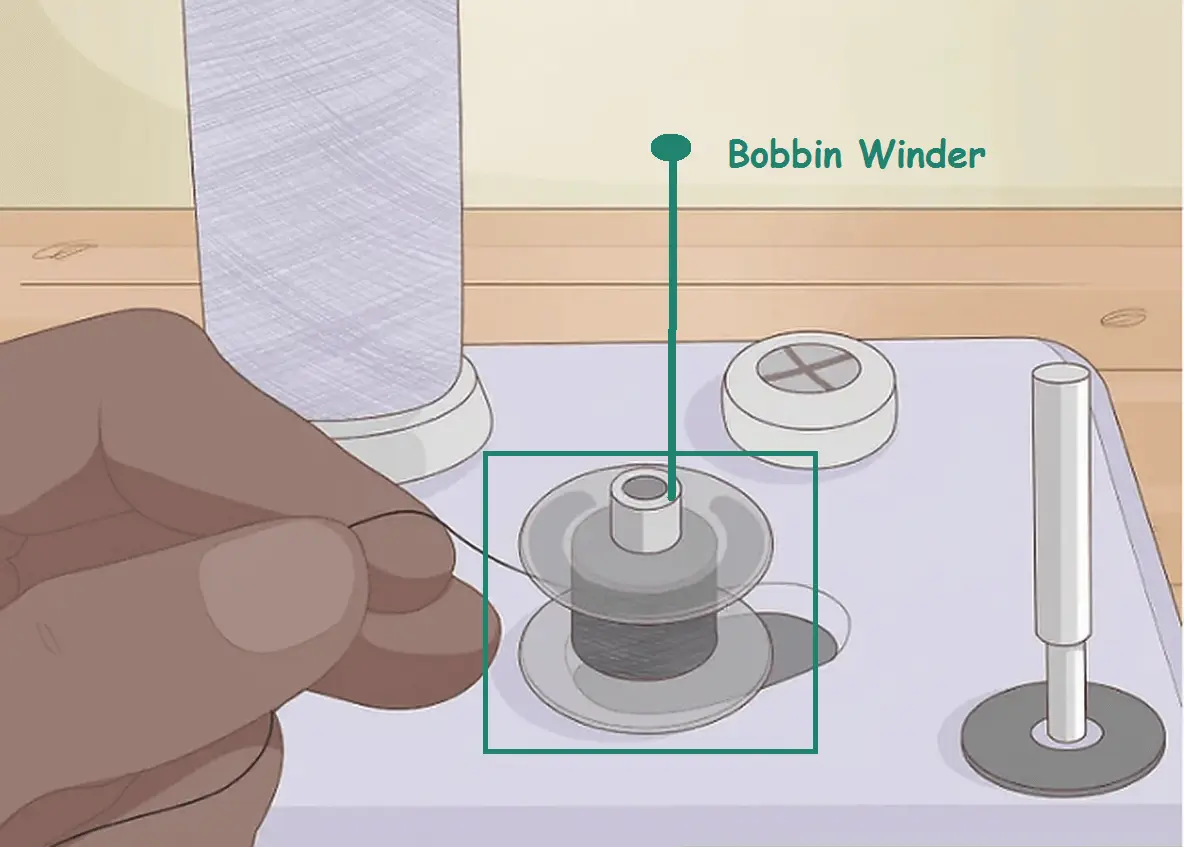
If you don’t have a pre-wound bobbin ready, now’s the time to make one. I always keep a few pre-wound bobbins in my sewing kit because there’s nothing worse than getting halfway through a project and realizing you need to stop and wind thread.
Pop your thread spool onto the spool pin, slide the bobbin winder pin to the left, thread the end through the little hole in your bobbin, and place it on the winder pin. Push the pin back to the right, then gently press your pedal to start winding.
Pro tip from someone who learned this the messy way: don’t go crazy with the pedal. Nice and steady does it. I once got overly enthusiastic and ended up with thread flying everywhere like some kind of craft store explosion.
Step 2: Load Your Thread Spool
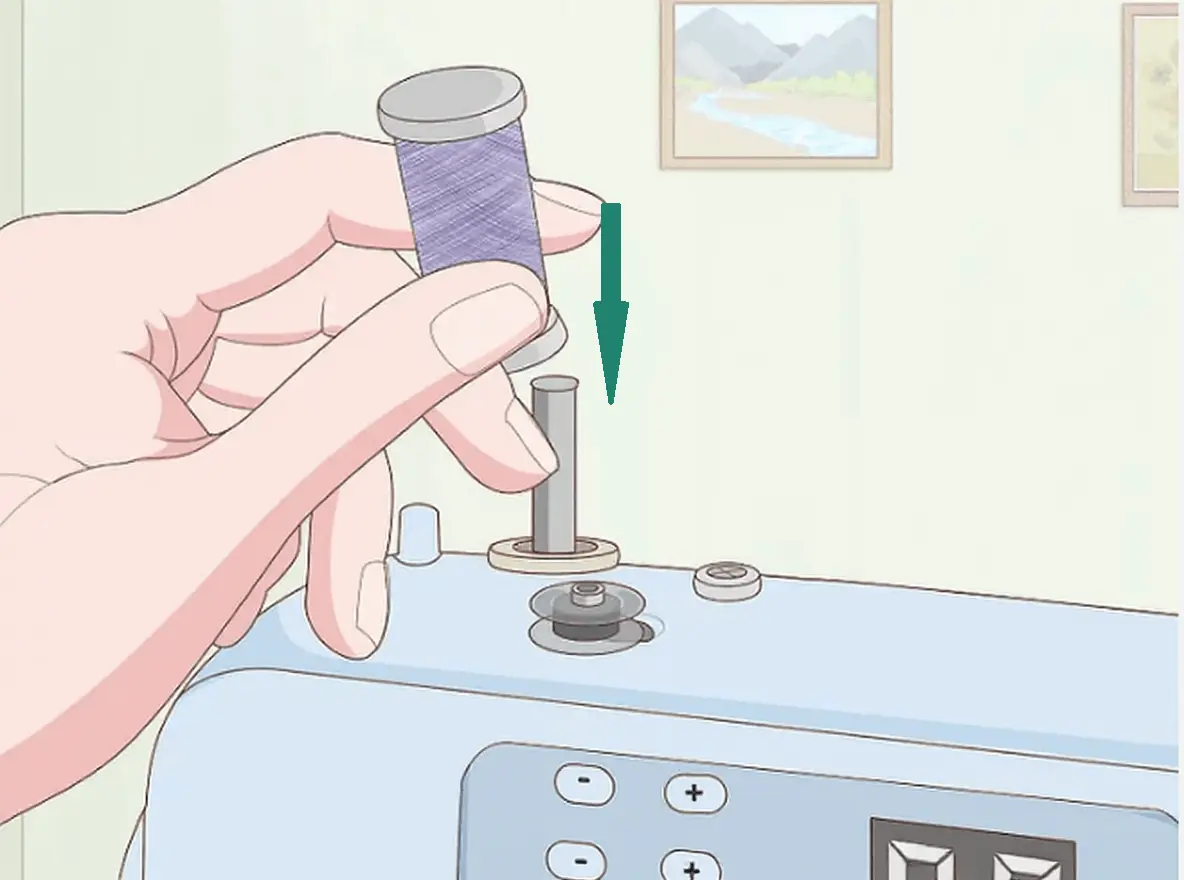
This part’s pretty straightforward. Take your thread spool and place it on the spool pin at the top of your machine. You should feel it click into place – that’s your confirmation that it’s secure.
If your Singer has a horizontal spool pin (some models do), don’t forget to put the cap on top. I forgot this step once and spent twenty minutes wondering why my thread kept getting tangled. Learn from my mistakes!
Step 3: Navigate the Thread Guide Maze
This is where things get interesting, and honestly, where most people get intimidated. But think of it like following a recipe – as long as you go in order, you can’t mess it up.
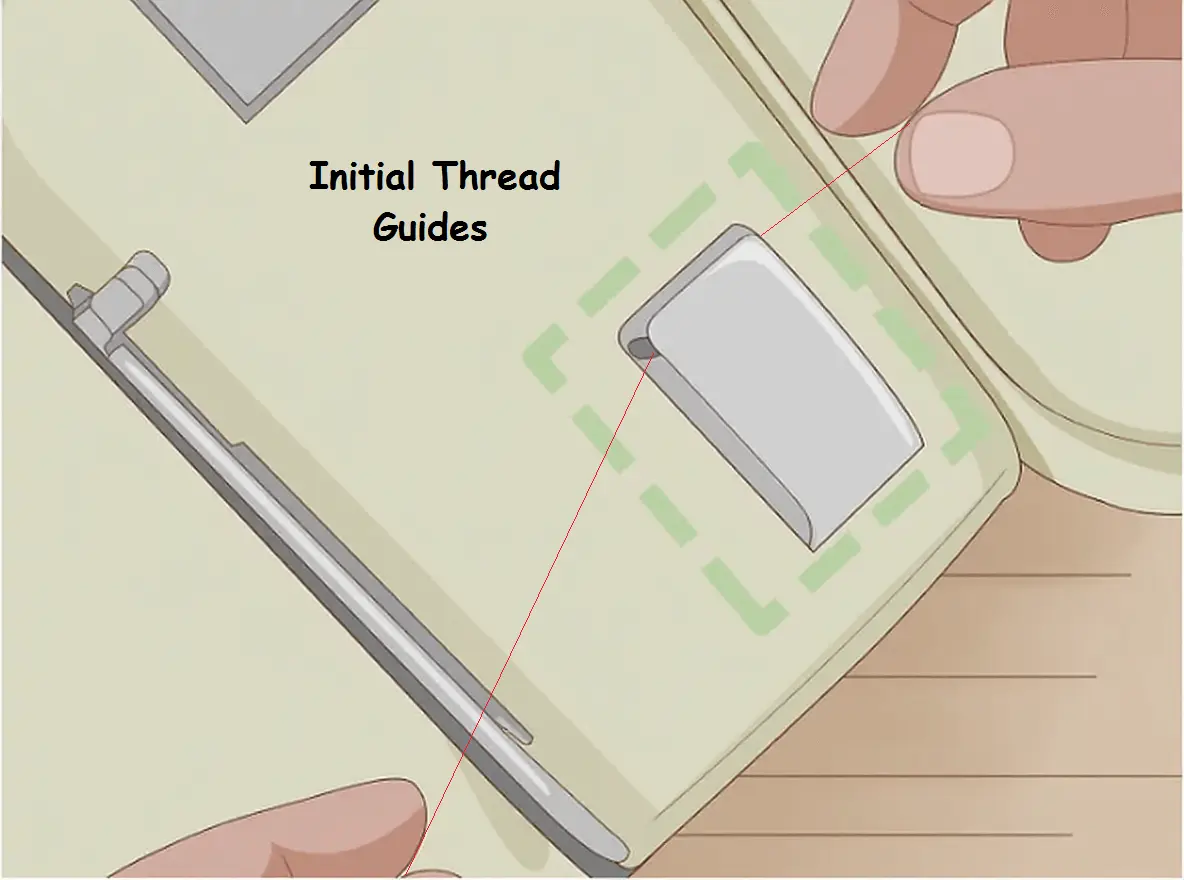
First, you’ll wrap your thread around the initial thread guide at the top of your machine. Pull the thread through the slot underneath, then wrap it over the top and around to the right side. The goal is to get that thread going through the guide and coming out on the right side.
Don’t overthink this part. I used to get so worried about doing it “perfectly” that I’d spend forever on this one step. As long as the thread is secured in the guide and flowing in the right direction, you’re golden.
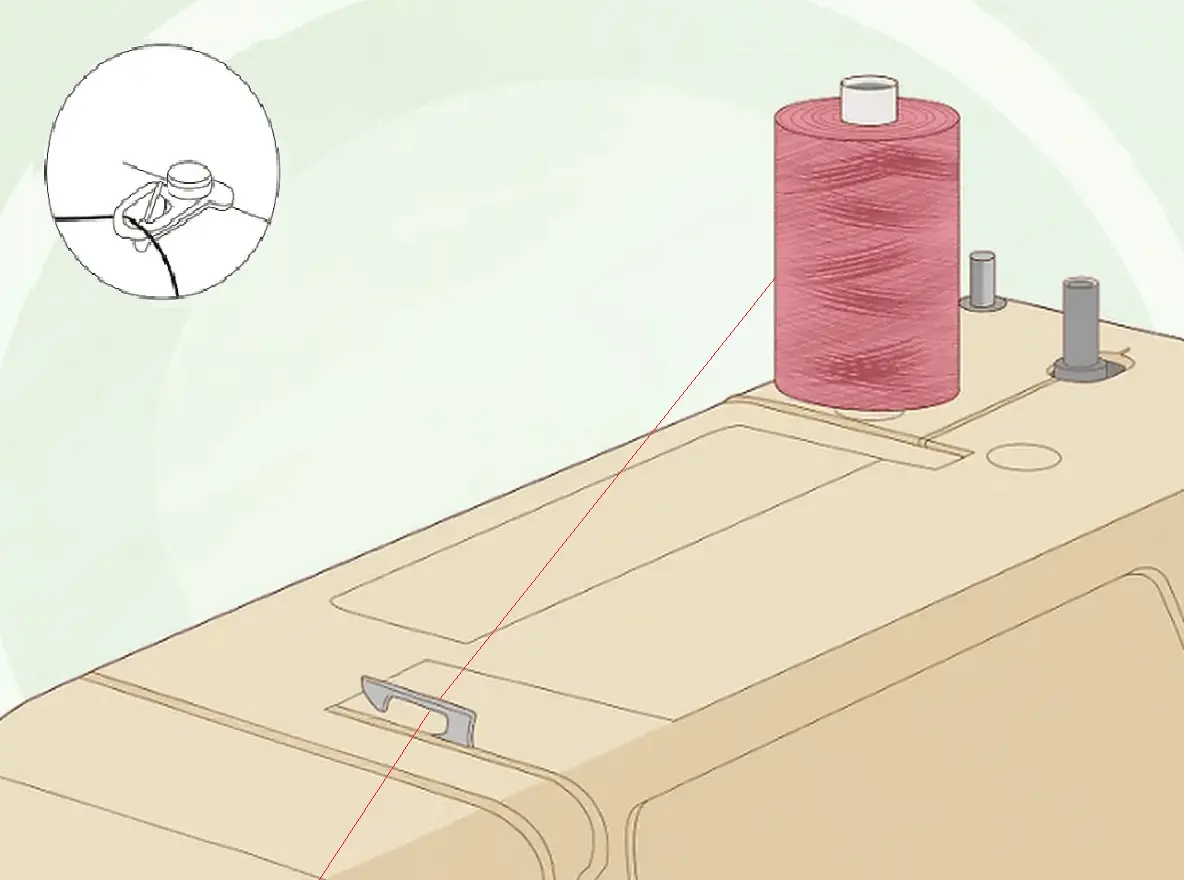
Next up is the second thread guide, which is right next to the first one. Go under the guide from the right side, bring the thread over the top, then slide it to the end of the guide to make sure it’s properly seated.
I’ll be honest – this felt super awkward the first few times I did it. My hands weren’t used to the motion, and I kept fumbling with the thread. But just like learning to type or ride a bike, your muscle memory kicks in eventually.
Step 4: The Threading Canal Challenge
Now we’re getting to the part that used to intimidate me the most – the threading canal. This grooved section on the side of your machine is where the real magic happens.
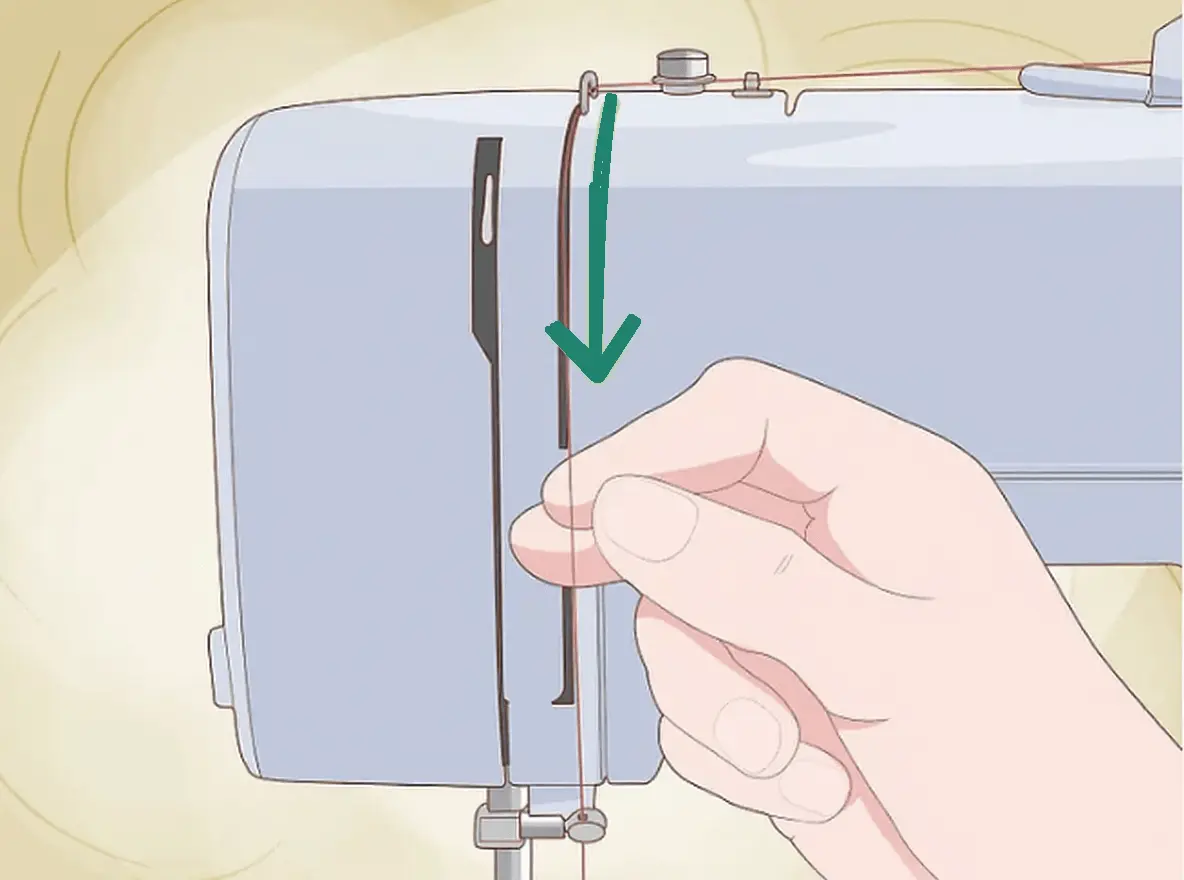
Pull your thread down through the canal and wrap it around the tension mechanism at the bottom. This little device is what keeps your stitches looking neat and professional instead of loose and sloppy.
Here’s something I wish someone had told me earlier: make sure your thread is straight and taut in the canal. I used to be too gentle, worried about breaking the thread, but a loose thread in the canal leads to wonky stitches later on.
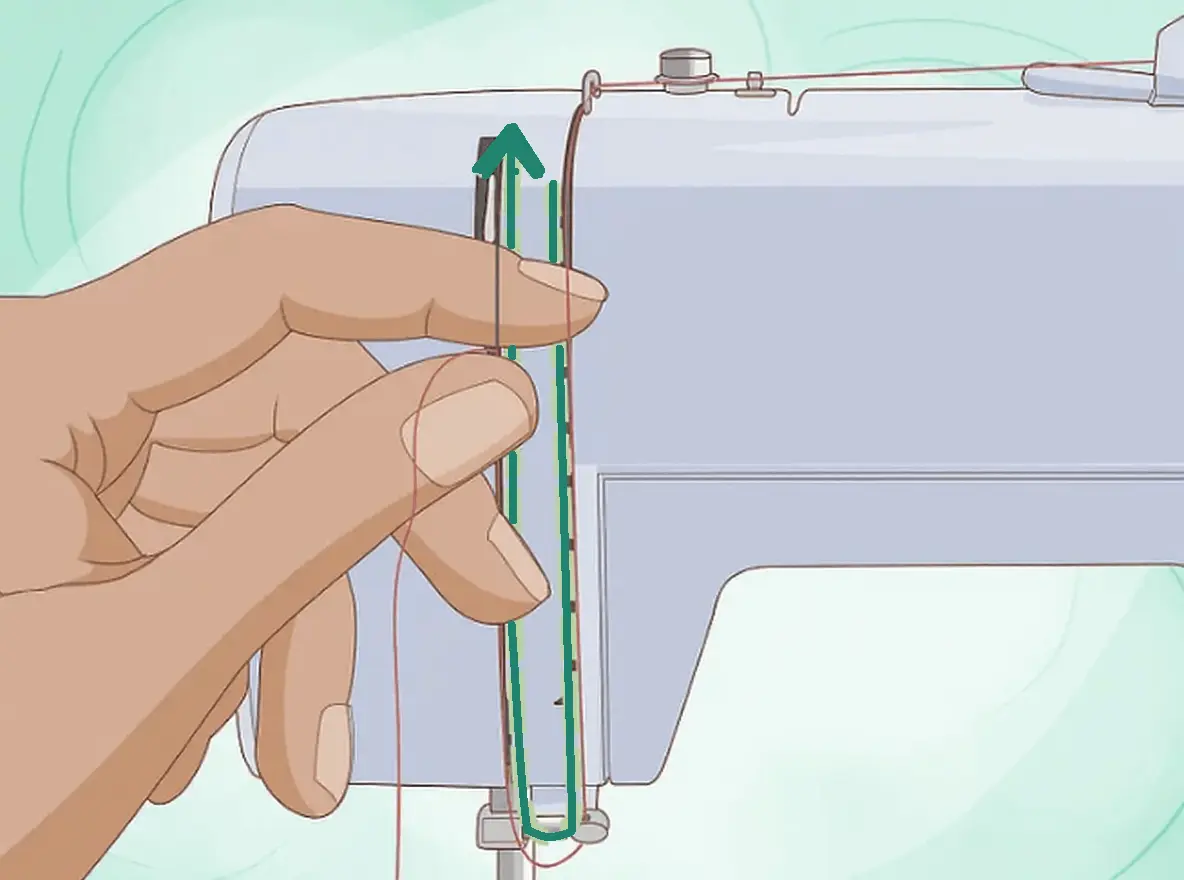
After you’ve got the thread through the tension mechanism, bring it back up the other side of the canal. At the top, you’ll thread it through the take-up lever. This little guy is another tension helper, so don’t skip it (I learned this the hard way).
Step 5: Almost There – The Home Stretch
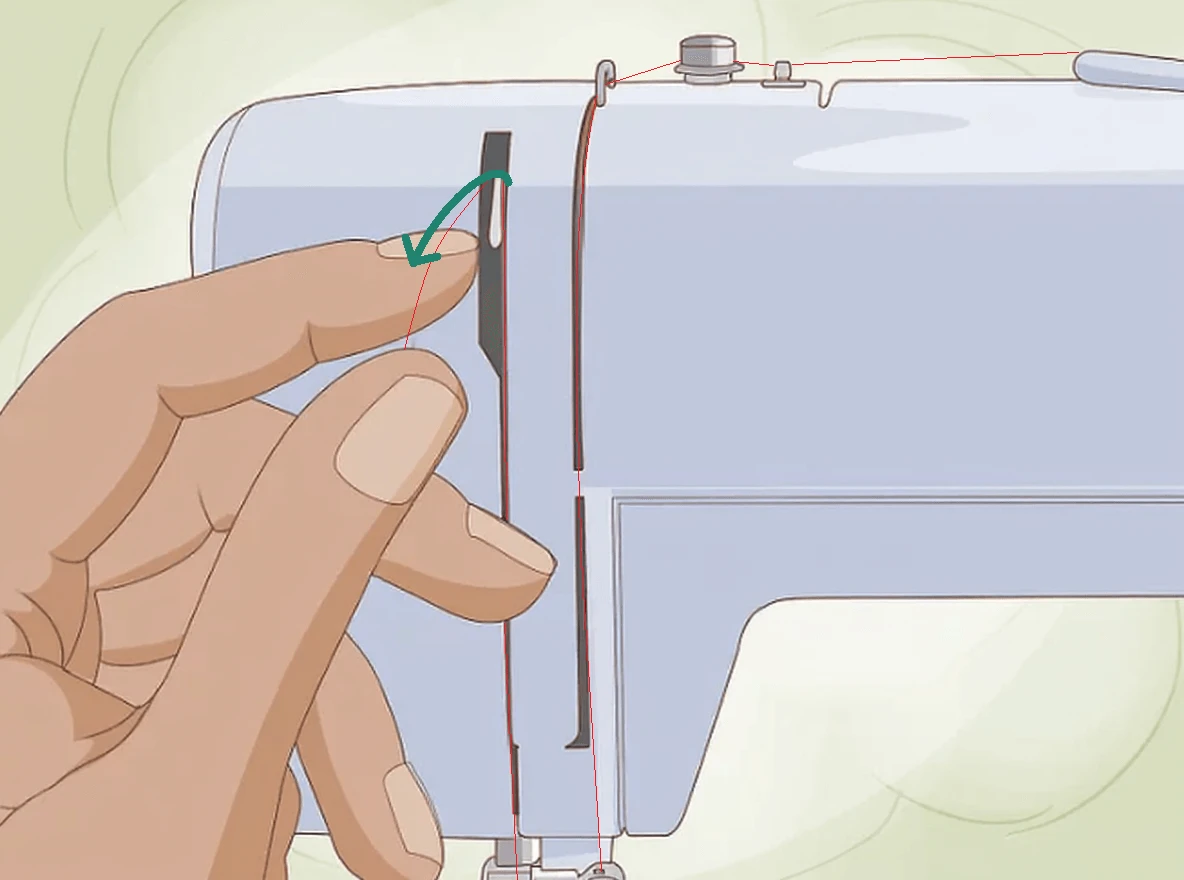
You’re doing great! Now pull the thread back down through the last section of the threading canal. When you reach the bottom, you’ll see a thread guide positioned right above the needle. Thread this guide – it’s your final checkpoint before the needle.
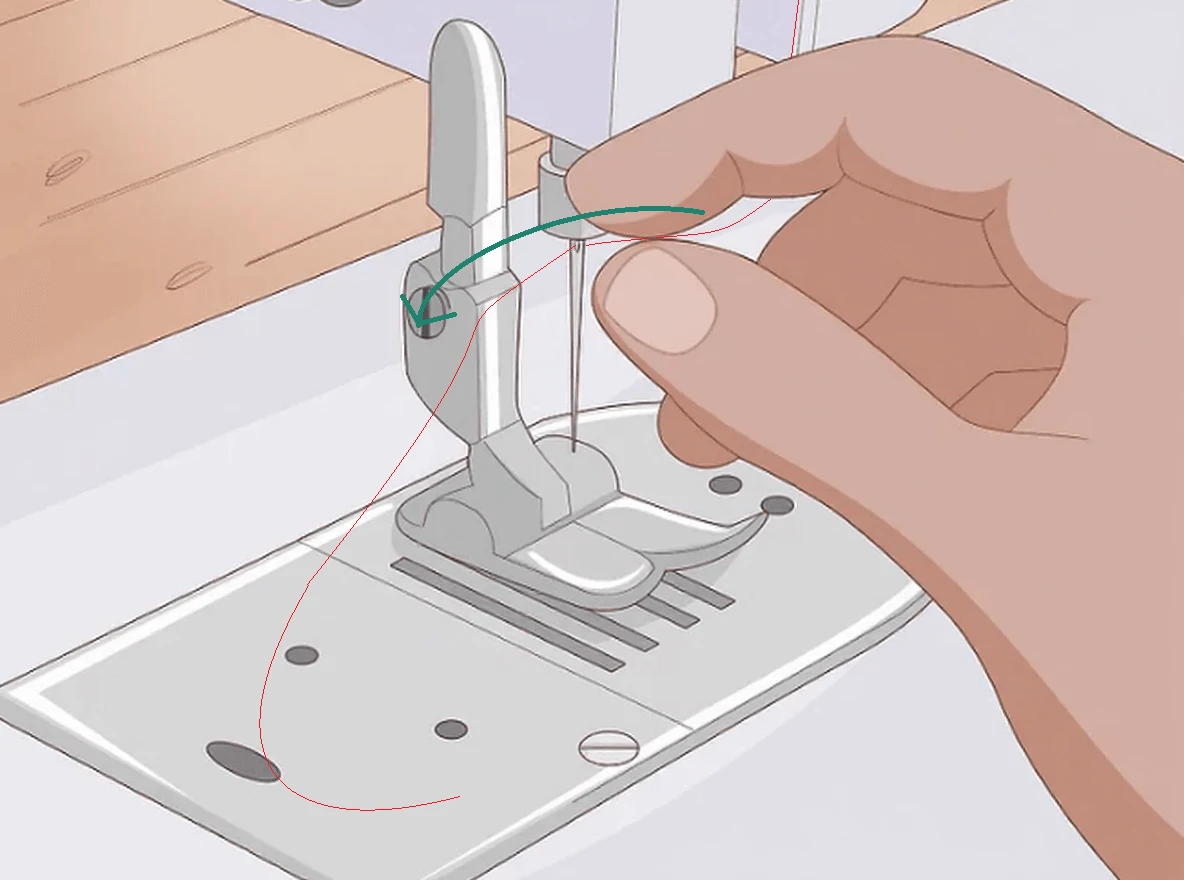
Now comes the moment of truth: threading the needle itself. Pull the thread straight down toward the needle’s eye, then push it through from front to back. Pull about 6 inches of thread through – this gives you enough working thread to get started.
Having trouble with this part? I totally get it. If your thread end is frayed (and let’s be honest, it usually is), just snip off about half an inch. You can also wet the thread end slightly to make it stiffer and easier to thread. Don’t worry, we’ve all done the “lick the thread” thing at least once!
Bobbin Time – We’re Almost Done!
Okay, we’re in the final stretch now. This is where everything comes together, and honestly, it’s pretty satisfying to watch your machine connect the top and bottom threads.
1. Check Your Needle Position
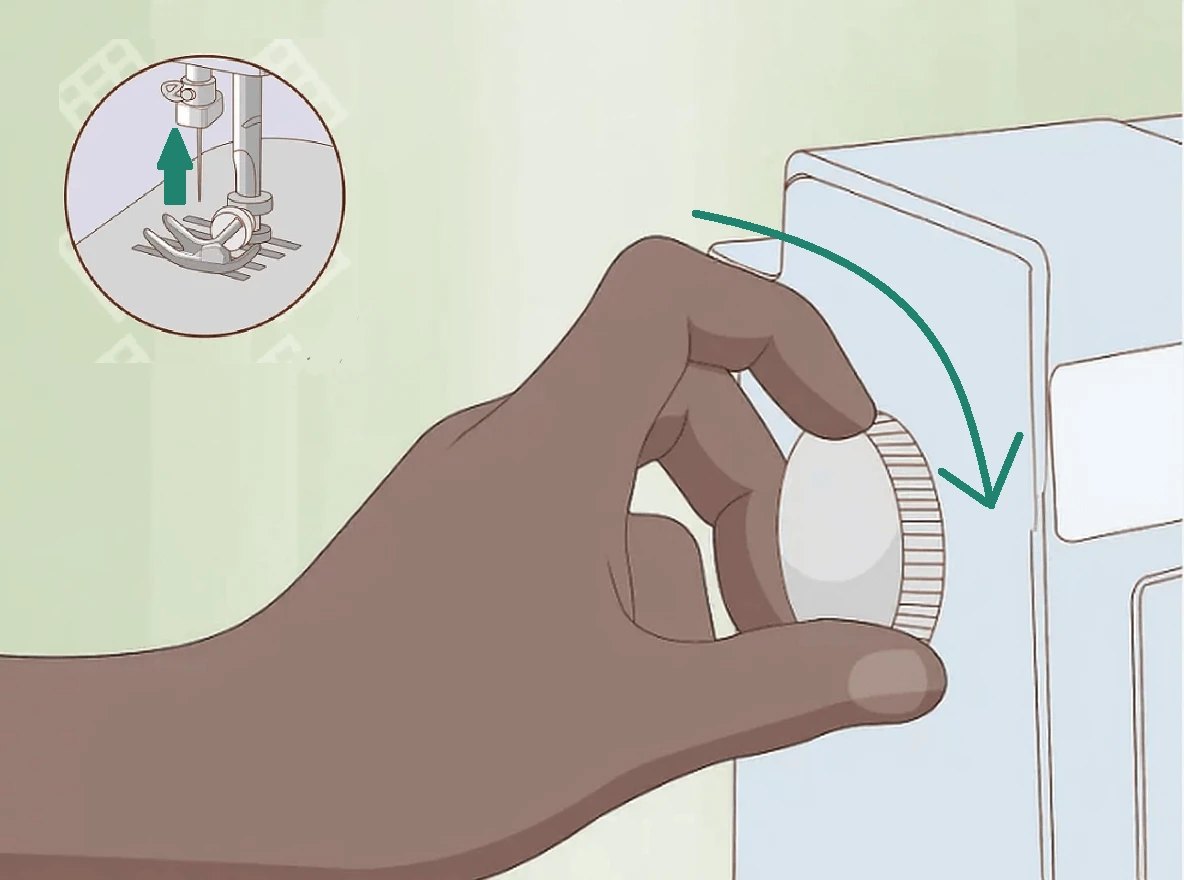
Make sure your needle is still in its highest position. If you’ve been following along, it should be, but if you’re not sure, just give the hand wheel a half-turn clockwise to raise it up.
2. Open Up That Bobbin Case
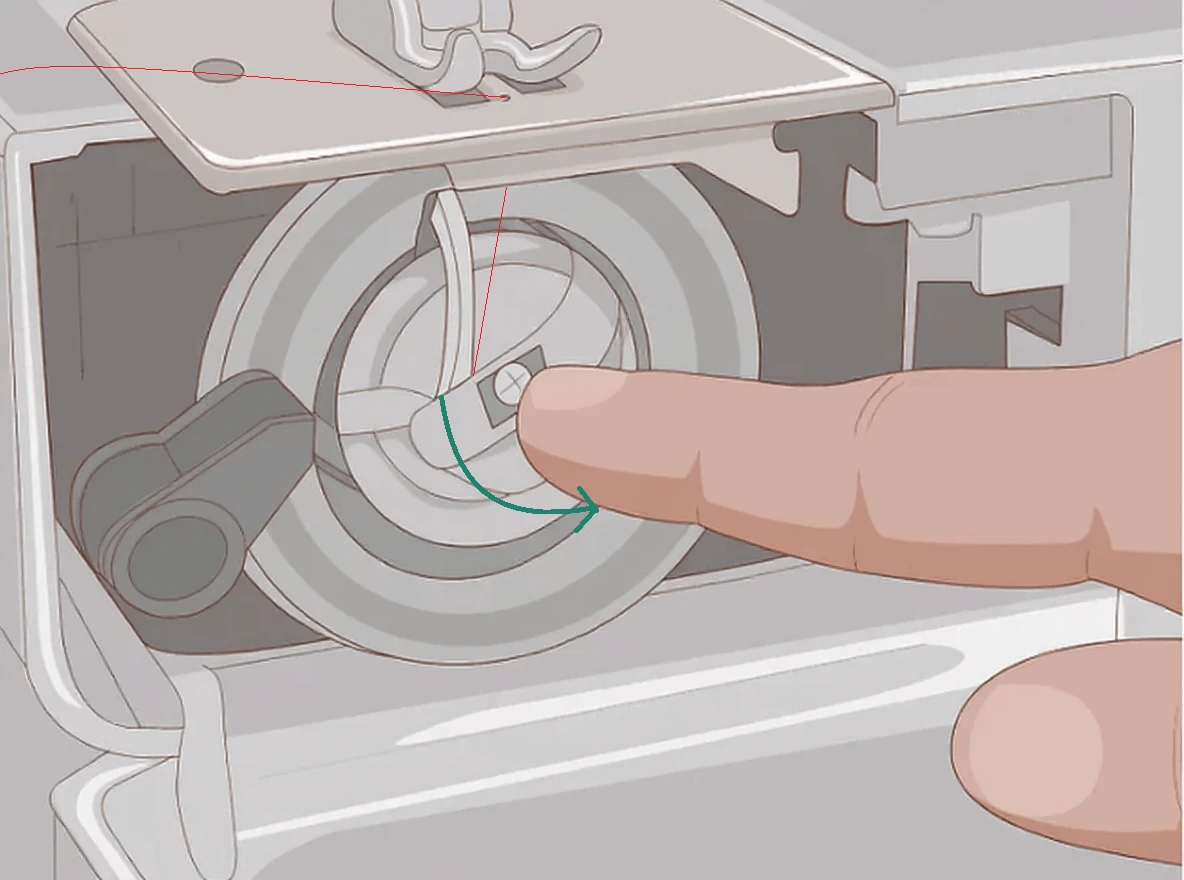
Look directly under your needle – you’ll see the bobbin case. There’s usually a button or tab that opens it. Press or lift to reveal the bobbin compartment.
If there’s an old bobbin hanging out in there, go ahead and evict it. We’re starting fresh with your newly wound bobbin.
3. Insert Your Bobbin the Right Way
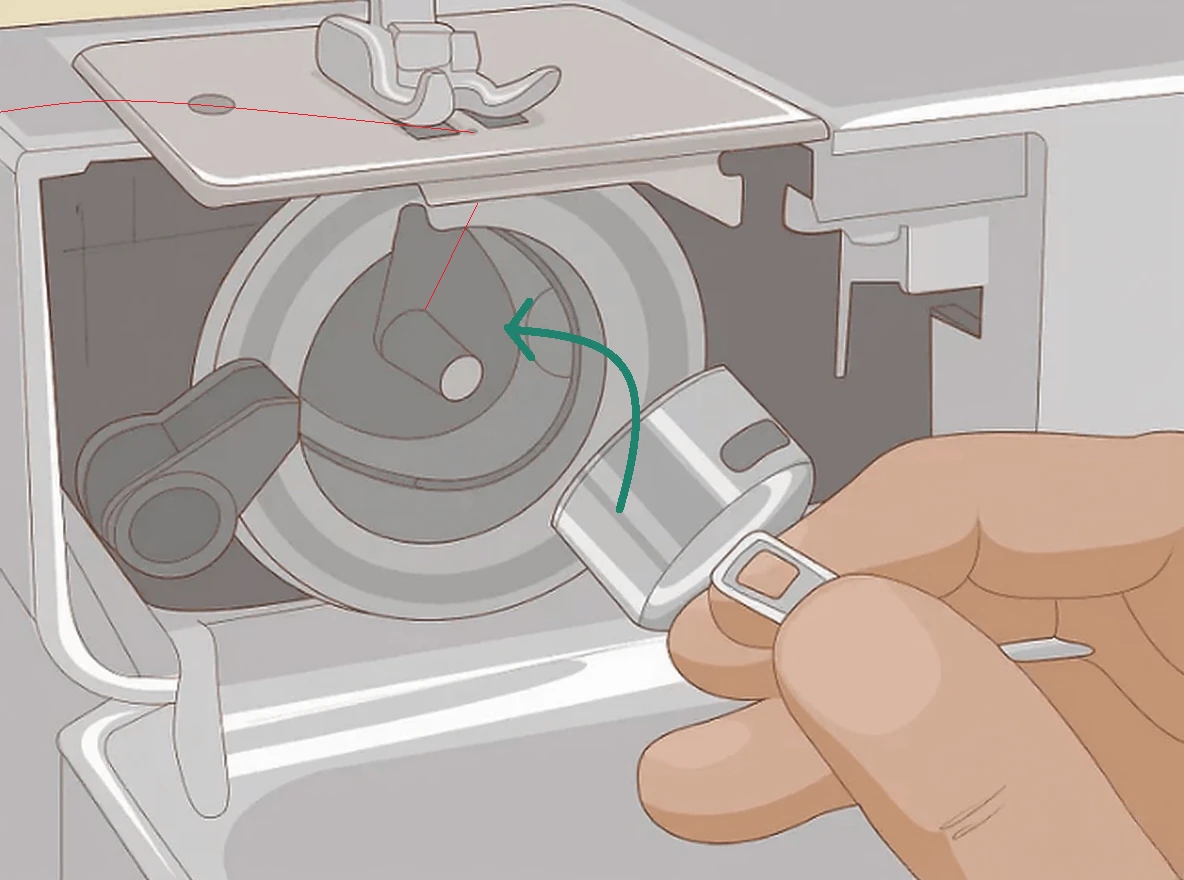
This is where those little arrows around the bobbin case become your best friends. They’re not just decoration – they’re telling you exactly which direction your thread needs to flow.
Place your bobbin in the case so the thread follows the arrow pattern. If the arrows show the thread going left, then up, position your bobbin so the thread flows in that exact direction. Getting this wrong is like trying to drive the wrong way on a one-way street – technically possible, but definitely not going to end well.
4. Pull the Thread Through the Slot
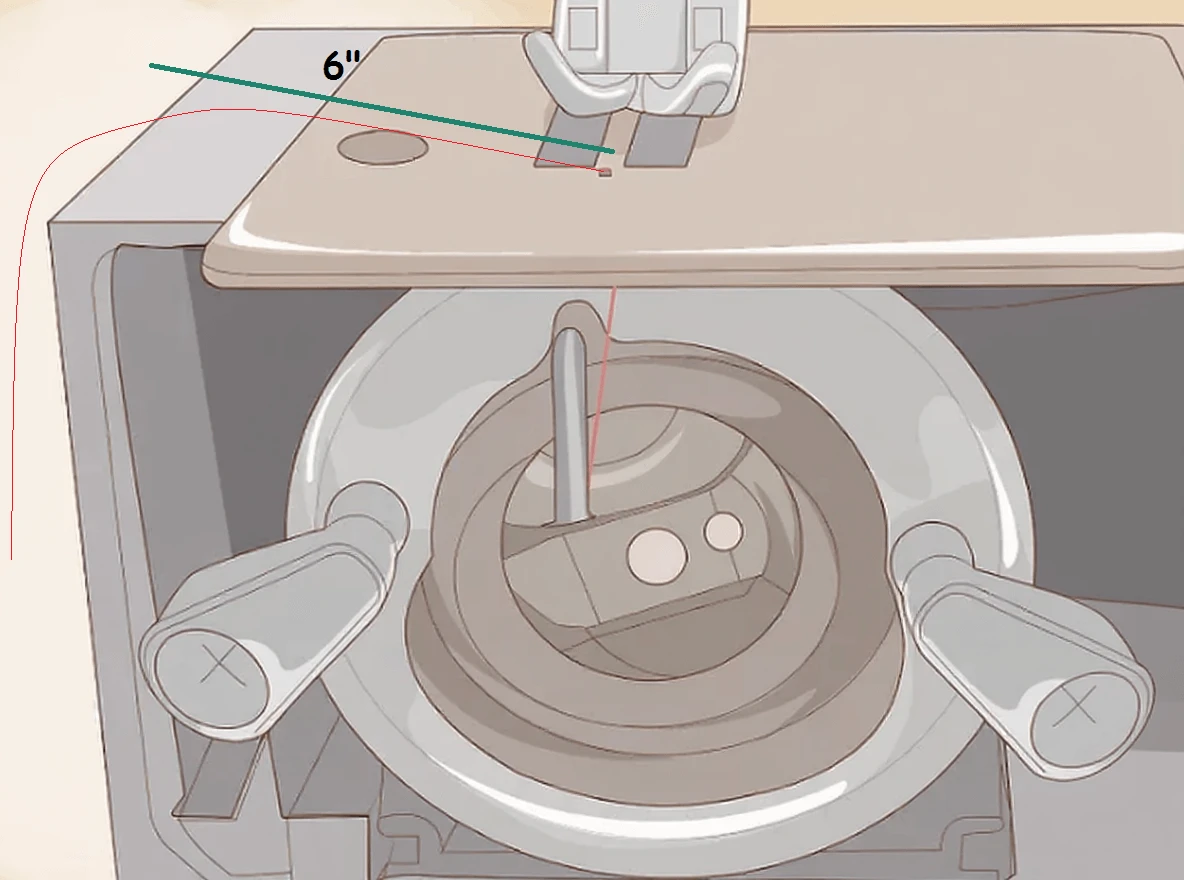
Pull about 6 inches of thread through the slot in the bobbin case. You don’t need to bust out a ruler – just eyeball it. This gives you enough thread for the next step and some extra to work with.
5. Close Everything Up
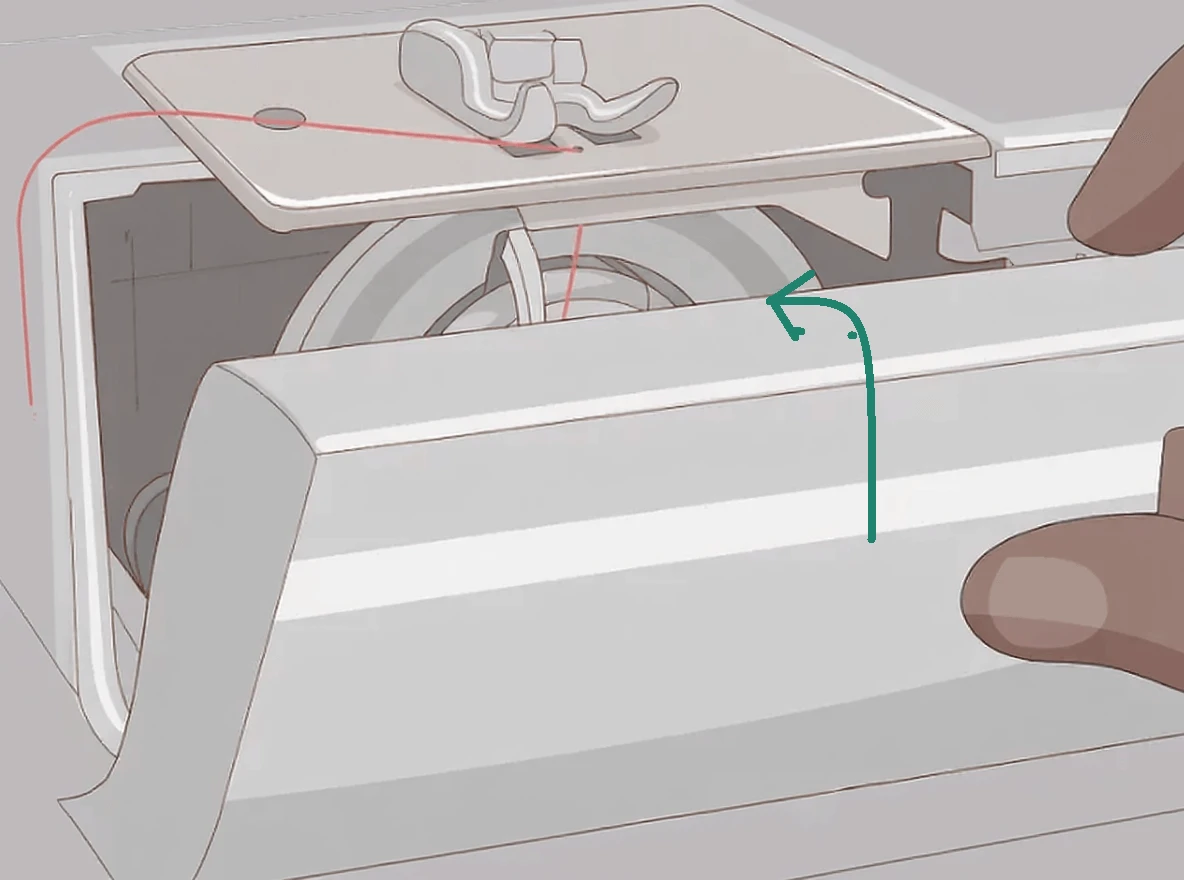
Snap that bobbin case lid back into place. You should hear or feel it click securely. If your Singer has a removable bobbin case, make sure to slide it back under the needle properly before closing.
6. The Magic Connection
This is my favorite part of the whole process. Turn the hand wheel clockwise a few times and watch as your machine pulls up the bobbin thread to meet the top thread. They’ll appear as a little loop – it’s like watching your machine shake hands with itself!
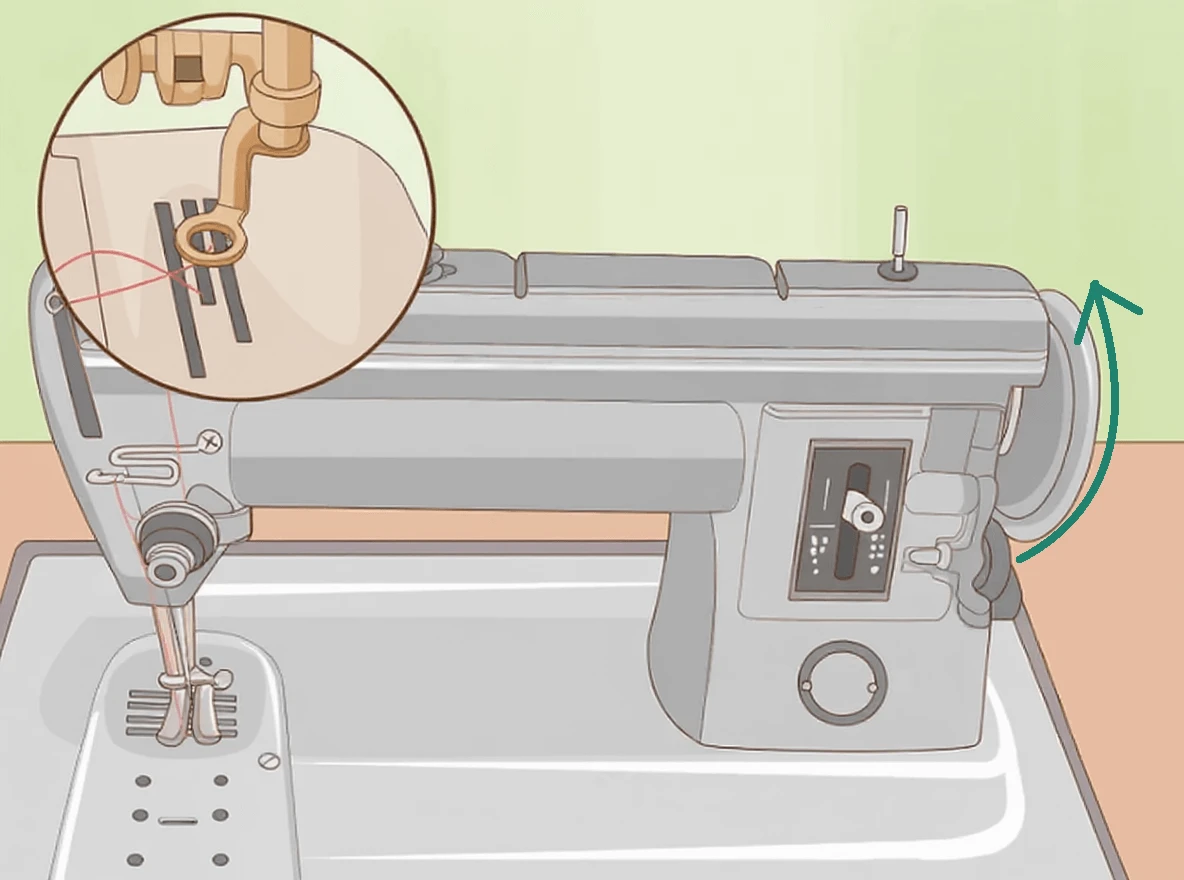
Gently pull the threads and push them to the back of the machine. If the thread doesn’t come up on the first try, don’t panic. Sometimes it takes a couple of attempts to get the timing right. I still occasionally have to do this twice, and I’ve been sewing for years.
When Things Go Sideways (Because They Will)
Let’s keep it real here – sometimes, threading doesn’t go according to plan. I’ve had my share of threading disasters, and I want to share some of the most common issues I’ve encountered (and how to fix them).
My thread keeps breaking: This was driving me crazy until I figured out it was usually because my tension was set too high. Also, the old thread is a brittle thread. I learned to invest in good-quality thread and store it properly. Cotton thread breaks more easily than nylon, so consider making the switch if you’re having constant breakage issues.
My stitches look terrible: Nine times out of ten, this means I missed a thread guide somewhere in the process. I’ve learned to double-check my threading path when my stitches start looking wonky. Even skipping one little guide can throw off your entire stitch quality.
My machine won’t stitch at all. This usually means either my top thread isn’t properly threaded, or I didn’t catch the bobbin thread correctly. When this happens, I just start over from the beginning. It’s faster than trying to troubleshoot what went wrong.
Remember, every single person who sews has dealt with these issues. The difference between a beginner and someone with experience isn’t that experienced sewers never have problems – it’s that they’ve learned how to fix them quickly and move on.
You’ve Totally Got This!
Look, I’m not going to lie to you – learning how to thread a Singer sewing machine properly takes practice. But you know what? So does riding a bike, cooking without burning things, and parallel parking. The key is being patient with yourself and remembering that every expert was once a beginner who felt completely overwhelmed.
The ability to thread a Singer sewing machine properly is truly the foundation of all your future sewing success. Once you’ve mastered this skill, you’ll approach every project with confidence. No more staring at your machine in confusion – you’ll thread it like the capable crafter you are. And if you’re still shopping for the perfect machine to complement your new threading skills, check out our guide to the best sewing machines to find your ideal match.
Here’s what I want you to remember: every beautiful quilt, every perfectly hemmed pair of pants, every gorgeous dress you’ve ever admired – they all started with someone threading their machine just like you’re learning to do right now.
Take your time with this process. Don’t rush. And for the love of all that’s holy, don’t get frustrated if you have to start over a few times. I promise you, there will come a day when you thread your Singer without even thinking about it. You’ll just sit down, thread it up, and start sewing like it’s the most natural thing in the world.
That day is coming sooner than you think. Until then, be kind to yourself, celebrate the small victories, and remember that every stitch you make is one step closer to becoming the seamstress you want to be.
Ready to give it a try? Thread up your Singer using these steps, grab a scrap of fabric, and take a few practice stitches. Then come back and tell me about your first successful threading experience – I genuinely love hearing these stories! Drop a comment below and let me know how it went.